1990 haben die zwei Schweizer Luc Dubois und J.P. Baudet die Zukunft der Segelherstellung aus einer anderen Perspektive betrachtet. In einem Hinterzimmer des North Sails Loft in Milford, CT (USA), vor neugierigen Blicken geschützt, hat Baudet wie ein High-Tech-Spiderman in einem Drachenfliegergeschirr über einer Holzform schwebend mit der Hand Kevlar-Fäden unter Spannung auf eine Mylar-Folie geklebt, die auf einer dreidimensionalen Holzform aufgebracht war. Ziel war es, ein perfekt geformtes J/24-Vorsegel aus einem 3D-Stück anstatt ein Segel mit unzähligen Nähten – wie es bei der traditionellen Art der Segelherstellung der Fall ist – zu formen. Etwa 4500 Meter Kevlar-Faden wurden sorgfältig ausgerichtet, damit sie den Lasten im Segel entsprechen. Baudet leistete harte Arbeit, um diese Fäden mit gleicher Spannung aufzubringen und dadurch die Form des Segels zu fixieren.
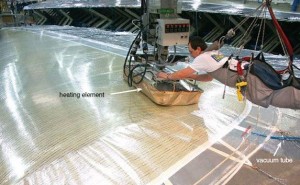
© North Sails
Es handelt sich hier um ein Verfahren, bei dem die Segel unter Hitze als einheitliche Membran auf einer 3-dimensionalen Form ihr Profil erhalten. Vorteil dieser Methode ist, dass die Fasern genau so gelegt werden können, wie die Kräfte auf das Segel wirken. Die laminierten Segel sind leichter und formstabiler. 3DL-Segel sind im America’s Cup marktbeherrschend. Elf von zwölf Teams am letzten Cup hatten 3DL-Segel.
Derzeit werden 3DL-Segel in der weltweit größten und am besten ausgestatteten Segelmacherwerkstatt in Minden, Nevada (USA) hergestellt von North Sails. Programmierbare Formen werden mit einer Mylar-Folie behängt; anschließend appliziert ein computergesteuertes System präzise die gespannte Faser auf dem Mylar. Weitere 3DL-Formen wurden kürzlich in der Produktionswerkstatt von North in Sri Lanka in Betrieb genommen.
Der Weltmarktführer North Sails zeigte auf der boot 2010 in Düsseldorf gleich zwei neue Innovationen aus der revolutionären 3DL-Produktreihe.